Hydrostatic transmissions – making sense of case drain flow – Part 1
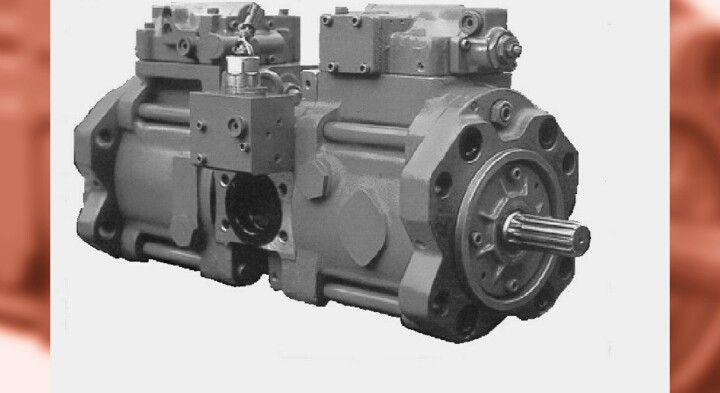
Hydrostatic transmissions – making sense of case drain flow – Part 1
November 10, 2015 Comments Off on Hydrostatic transmissions – making sense of case drain flow – Part 1One of our readers recently wrote to me regarding the following problem:
What is a hydrostatic transmission?A hydrostatic transmission consists of a variable-displacement pump and a fixed or variable displacement motor, operating together in a closed circuit. In a closed circuit, fluid from the motor outlet flows directly to the pump inlet, without returning to the tank. As well as being variable, the output of the transmission pump can be reversed, so that both the direction and speed of motor rotation are controlled from within the pump. This eliminates the need for directional and flow (speed) control valves in the circuit. Because the pump and motor leak internally, which allows fluid to escape from the loop and drain back to the tank, a fixed-displacement pump called a charge pump is used to ensure that the loop remains full of fluid during normal operation. The charge pump is normally installed on the back of the transmission pump and has an output of at least 20% of the transmission pump’s output. In practice, the charge pump not only keeps the loop full of fluid, it pressurizes the loop to between 110 and 360 PSI, depending on the transmission manufacturer. A simple charge pressure circuit comprises the charge pump, a relief valve and two check valves, through which the charge pump can replenish the transmission loop. Once the loop is charged to the pressure setting of the relief valve, the flow from the charge pump passes over the relief valve, through the case of the pump or motor or both, and back to tank. What is the significance of case drain flow?When a pump or motor is worn or damaged, internal leakage increases and therefore the flow available to do useful work decreases. This means that the condition of a pump or motor can be determined by measuring the flow from its case drain line (internal leakage) and expressing it as a percentage of its theoretical or design flow. How does this apply to hydrostatic transmissions?When applying this technique to a hydrostatic transmission, charge pump flow must be considered. In most transmissions, the charge pump relief valve vents into the case of either the pump or the motor. This means that in the circuit described by our reader, where the motor case drain flushed through the transmission pump case to tank, you would expect to see the flow meter in the transmission pump case drain line reading design charge pump flow. Here’s why: Say charge pump flow was 10 GPM, of which 4 GPM was leaking out of the loop through the motor’s internals (case drain) and 2 GPM was leaking out of the loop through the pump’s internals. The balance of 4 GPM must therefore be going over the charge relief – but still ends up in either the pump or motor case, depending on the location of the relief valve. In this particular circuit, because the motor case drain flushed through the transmission pump case to tank, you would expect to see the flow meter in the transmission pump case drain line reading the sum of these three flows (10 GPM). Before any meaningful conclusions can be drawn, the case in which the charge pump relief is venting (motor or pump) must be determined and the two case drain lines (motor and pump) must be isolated from each other. If the charge relief vents into the case of the pump, then it is possible to determine the condition of the motor by measuring its case drain flow, but not the pump. If the charge relief vents into the case of the motor, then it is possible to determine the condition of the pump by measuring its case drain flow, but not the motor. It is not possible to determine the condition of the component that has the charge relief valve venting into it because there is no way of telling what proportion of the total case drain flow is due to internal leakage – unless of course the charge relief can be vented externally while the test is conducted. While it is possible to do this on most transmissions, it’s not usually a simple exercise. Using case drain flows to determine the condition of the components of a hydrostatic transmission, without a thorough understanding of closed circuits, can result in incorrect conclusions and the costly change-out of serviceable components. Â Copyright 2003 — Insider Secrets to Hydraulics ABOUT THE AUTHOR:Â Brendan Casey has more than 16 years |
|||||||||||||||||||||||||||||||||
Need Hydrostatic Parts Call Us ! | |||||||||||||||||||||||||||||||||
For a list of our Eaton pumps and prices, go to our Eaton hydrostatic parts page
Or visit us at our EBay store: Hydrostatic Transmission Service, LL |
|||||||||||||||||||||||||||||||||
HYDRAULIC REPAIR – HYDROSTATIC PUMPS – HYDROSTATIC EQUIPMENT | |||||||||||||||||||||||||||||||||
CALL US FOR YOUR REPAIR ON DIFFICULT TO LOCATE HYDROSTATIC TRANSMISSION REPAIR.
MITSUBISHI, KAWASAKI, DAEWOO ,DYNAPOWER, LINDE, REXROTH, UCHIDA, YAMAHA, HITACHI, KOMATSU, LIEBHERR, POCLAIN, VOLVO, VICKERS, CESSNA, HYDROMATIK AND SUNDSTRAND AND EATON CLOSED LOOP AND OPEN LOOP HYDROSTATIC DRIVE PUMPS AND MOTORS. |
|||||||||||||||||||||||||||||||||
(800) 361-0068
hydrostaticpumprepair.com
|